What You Need to Make Your Smart Products Attract Attention
In the ever-evolving environment of technology and innovation, those in the functional electronics industry are confronted with the need to not only keep pace but to stand out among competition. As we dive into the world of in-mold structural electronics (IMSE®), also referred to as in-mold electronics (IME), it is clear that improving the customer experience through innovative technology is not just a consumer preference but a strong strategic move for those wanting a competitive edge with their smart products.
Where do your challenges lie?
Balancing design creativity with manufacturing feasibility is challenging, especially when one wants to stand out from the competition. This isn’t the case with in-mold structural electronics. IMSE is an advanced molding technology that allows for flexibility in design. Designers are given the space to be creative in their product design with more opportunity for unique attributes, such as haptics, LEDs, capacitive touch and so much more.
With IMSE, engineers do not have to worry about reaching technical limitations. IMSE removes many typical design and manufacturing obstacles, so we are left with a smart, functional and aesthetically pleasing product for customers. IMSE allows manufacturers to easily design variants of a single product and to continuously reinvent the product to stay ahead in the game.
Why IMSE for you and your customers?
Appearance: Allows for the incorporation of electronic components, such as haptics, touch controls and LEDs, directly into the molded part. This helps maintain a sleek and uncluttered appearance that is perfect for many industries, including automotive and appliance.
Durability: Electronic components are molded within the structure of the part, adding protection against external elements. Parts produced with IMSE contain no moving parts, which protects the part from breaking.
Streamlined production: IMSE combines structural and electronic elements in a single molded part, eliminating the need for separate assembly steps. This reduces production complexity and potential points of failure.
Design freedom: The IMSE process enables the design of products with integrated electronic features without compromising aesthetics. Designers have more freedom to create innovative and advanced product designs.
Cost efficiency: Integrating graphics and electronic features during the molding process reduces the need for additional assembly steps, saving on labor and material costs.
Space optimization: Integrating electronics within the structure of the product saves space and eliminates the need for separate electronic enclosures, contributing to a more compact, durable and lightweight design.
Improved functionality: IMSE introduces electronic functionalities, such as touch controls, lighting and haptics, directly into the product, improving user interaction and overall performance.
Differentiation in the market: IMSE is a unique, high quality and technically advanced solution. Adopting this process will differentiate you from your competitors.
How DuraTech ensures quality in IMSE
Quality, especially in high-tech processes like IMSE, is incredibly important. IMSE requires precision and consistency when integrating electronics into structural components. Every smart interface demands functionality, reliability and high performance.
“The importance of quality assurance in high-tech projects like IMSE cannot be overstated. In these projects, the stakes are high as the products are often used in critical applications where failure is not an option. Quality assurance serves as a safeguard, ensuring every product is reliable, safe, and performs as intended. This not only protects the end user but also reinforces our standing as a company devoted to excellence in every facet of our operations.” Kasey Cockroft, Assistant Team Leader of Quality Assurance.
Collaboration is key
Collaboration with DuraTech in adopting IMSE goes beyond the immediate advantages, offering smart, innovative solutions that align with consumer needs. It is a priority to understand our customer’s unique requirements so that we can ensure the final product adheres to your customer’s specifications. In addition to collaboration, open communication is equally important. A continuous dialogue ensures that needs and concerns are addressed promptly, keeping the project on track with your timeline.
DuraTech will support your journey to the top
At DuraTech, we continuously demonstrate our expertise in innovation, problem-solving and delivering quality. Our team excels in specialized solutions for the most intricate challenges, leading to the inception of IME technology. Hear directly from one of our customers about their experience and explore the following case study to see how our team has overcome unique challenges.
Watlow
Watlow and DuraTech collaborated to innovate one of the first in-mold electronics (IME) products in the United States, aiming to enhance the durability of an industrial controller. The project, initiated in 2018, involved embedding flexible printed circuits between plastic layers to achieve waterproofing, reduced weight, and improved reliability. DuraTech contributed expertise in faceplate development, while Watlow focused on the electronics, resulting in the Watlow PM Plus™ industrial controller with Bluetooth compatibility and an intuitive interface.
The collaboration faced challenges, including visible marks on the front surface during molding, which were overcome through the development of unique ink systems and molding processes. The success of the project showcased the viability of IME production methods for creating quality, durable products. The dedicated team from both companies fostered trust through close collaboration, emphasizing DuraTech’s commitment to customer service. Going forward, DuraTech engineers will refine IME processes based on this successful collaboration with Watlow, marking a significant milestone in the application of this innovative technology. For the complete case study, refer to the detailed account of the Watlow and DuraTech collaboration.
DuraTech is a licensee of TactoTek’s IMSE technology
DuraTech Industries has obtained a license for TactoTek®’s in-mold structural electronics (IMSE®) technology, empowering the company to sell, design, and produce IMSE parts using TactoTek’s intellectual property. Specializing in in-mold electronics (IME) already, DuraTech aims to enhance electronic functionality, incorporating features like LEDs and system-in-package (SiP) electronics within 3D injection molded structures. The collaboration allows DuraTech to expand its offerings globally, responding to increasing customer demands for advanced electronic features in IME parts, with production facilities based in the USA.
TactoTek’s IMSE technology, recognized for integrating electronic components into 3D injection molded structures, aligns with DuraTech’s mission to reliably mass-produce high-quality IMSE solutions for diverse markets, including home appliances, medical, industrial, automotive and consumer electronics. The licensing agreement supports TactoTek’s go-to-market strategy for IMSE technology and opens new business opportunities for DuraTech, bringing innovative smart surfaces to various industries worldwide.
Read the full press release here.
Make the switch your customers want
The proactive adoption of in-mold structural electronics distinguishes you from your competitors. This adoption not only addresses the challenge of design creativity and manufacturing feasibility, but positions you to provide the smart products your customers look for.
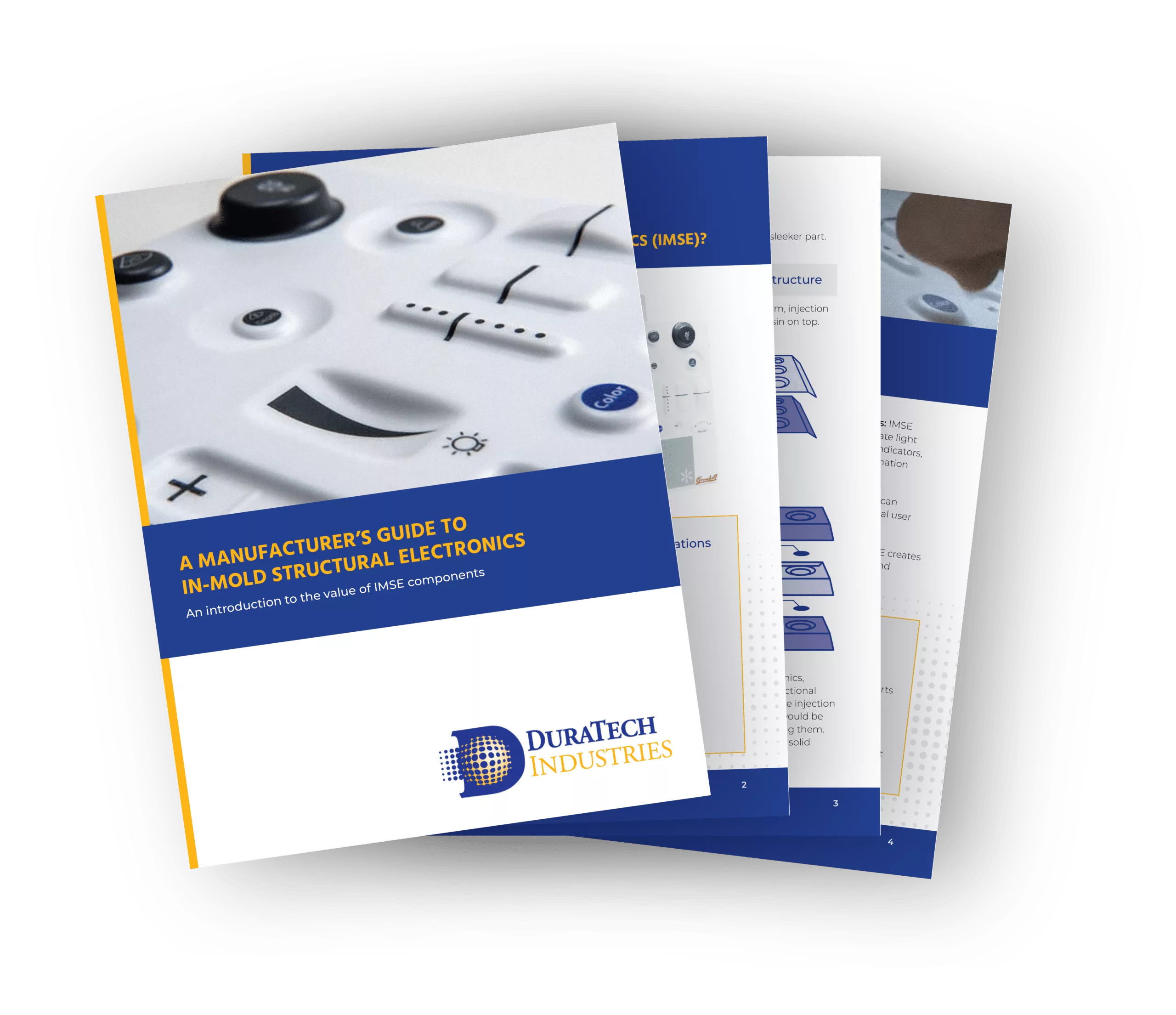
Download our ebook to gain insights and tips that empower you to make the switch to IMSE.
A Manufacturer’s Guide to In-Mold Structural Electronics
Known as the perfect union of form and function, IMSE integrates printed, conductive inks with In-Mold Decorating (IMD). It produces a single finished product that requires a fraction of the space of conventional electronics and eliminates the need for a printed circuit board (PCB).
The graphic and functional inks are printed second surface so they are protected behind the applique substrate. IMSE products are
typically printed on polycarbonate and polyester, but DuraTech is not limited to these materials.
IMSE is a low-cost alternative to traditional technologies and requires fewer raw materials and zero assembly while improving product durability and the user experience.