Printed electronics (PE)
DuraTech creates custom printed electronics solutions
We Print Science ℠
Printed electronics (PE) is a rapidly growing field that involves the use of printing techniques to produce 3d printed electronic components such as sensors, displays, batteries and flexible printed circuits. Screen printing is a popular method used to produce printed electronics products, as it is cost-effective and can be used to produce large quantities of components quickly.
Types of materials used in printed electronics technology
Substrates
Flexible substrates, such as plastics and papers are typically used to produce devices that use printed electronics. These substrates offer a high degree of flexibility and can be produced in any shape or size.
Inks
Conductive inks are used in printed electronics applications. Inks typically used at DuraTech include silver conductive ink and dielectric inks that provide insulation as part of the printed circuit stack. These inks are used to produce electronic components such as printed flexible circuits and sensors.
Adhesives
Adhesives are generally used to attach the electronic components to the substrate since most substrates don’t tolerate the soldering process. These adhesives offer a high degree of flexibility and can be customized to fit the specific needs of the application.
What’s going on inside a printed electronics part?
Parts DuraTech manufactures in our printed electronics department are made in layers. In an average part, you’ll see layers consisting of conductive inks, LEDs and other electronic features, graphic overlays and dome actuators.
For those parts that are clean critical, we use a clean room for production and assembly. DuraTech’s clean room allows us to complete work commonly restricted to certified Class ISO 6 (comparable to Class 1,000). Processes like Dry Film Bonding, Liquid Optical Bonding and the manufacturing of Optical Filters are possible in our clean room.
Printed electronics industry has a wide range of applications
Printed electronics is finding applications in a variety of industries, including medical, automotive, consumer electronics and more.
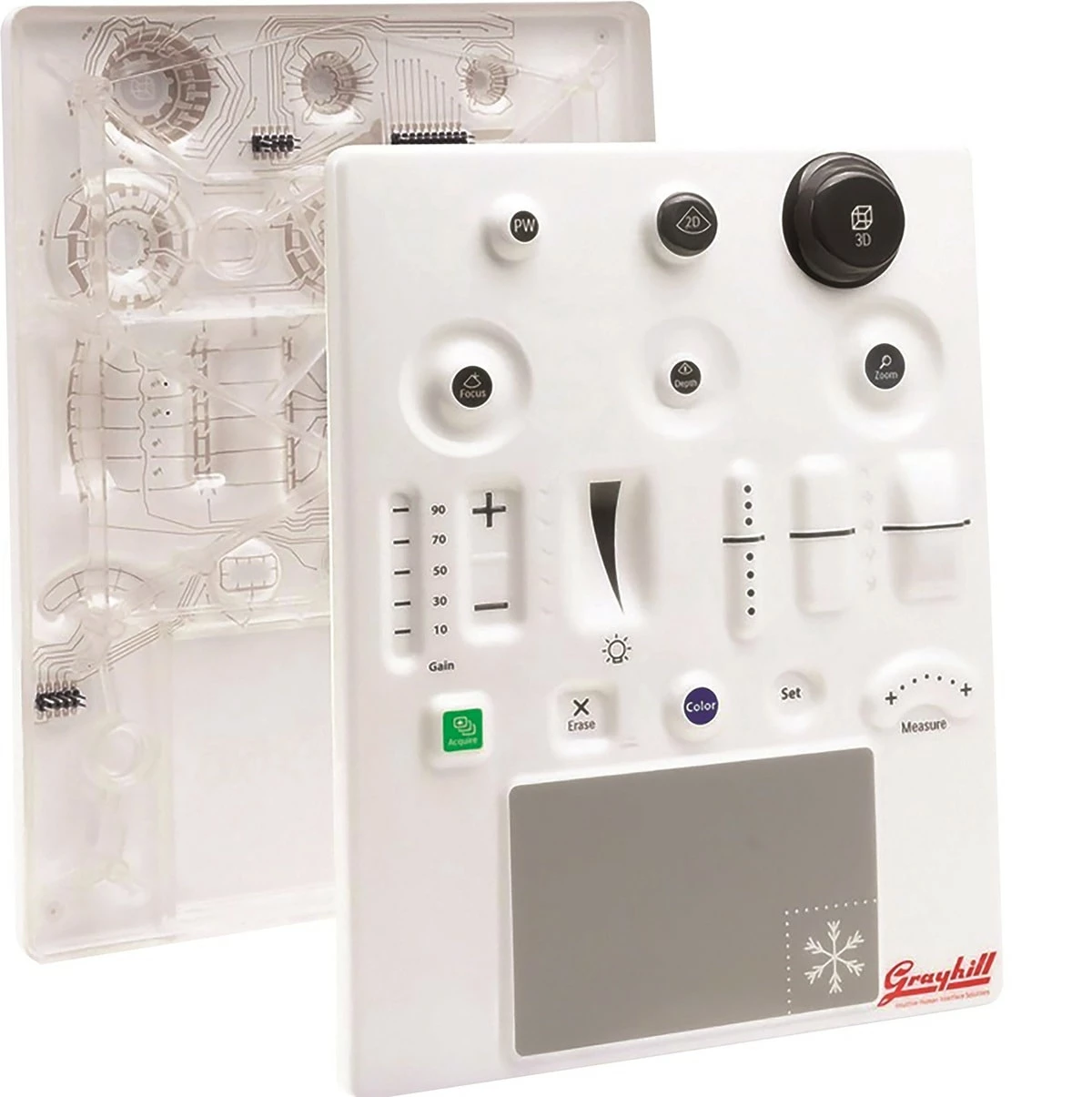
User interface products
Printed electronics products are commonly used in the production of user interface products, such as touchscreens, buttons and membrane switches. These products can be customized to fit the specific needs of the application, and they offer a high degree of design flexibility.
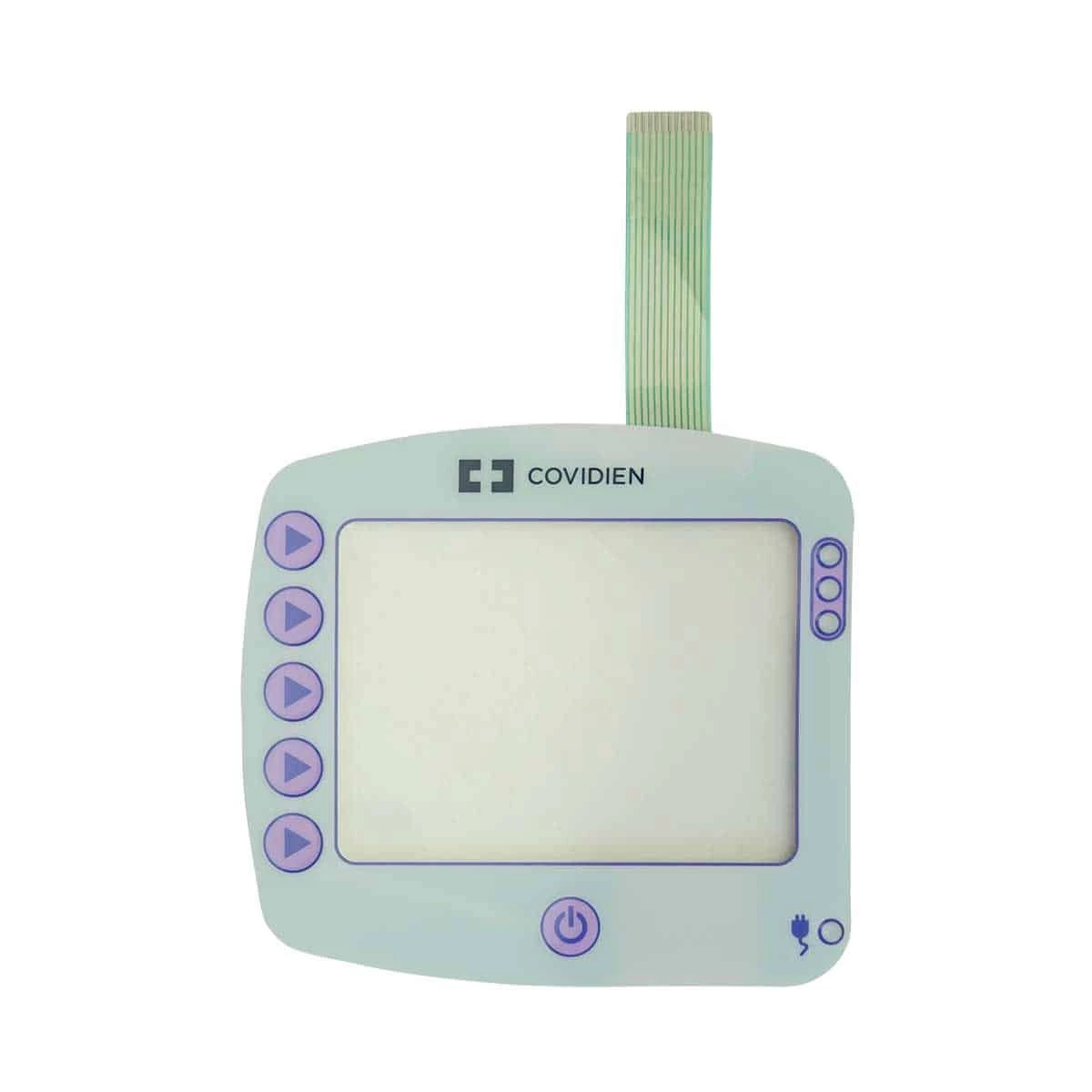
Medical devices
The production of medical devices, such as biosensors and electronic bandages that can monitor wound healing, are a good candidate for the printed electronic process. It can also be used to create flexible, lightweight and conformable healthcare electronics, making them ideal for wearable and portable applications.
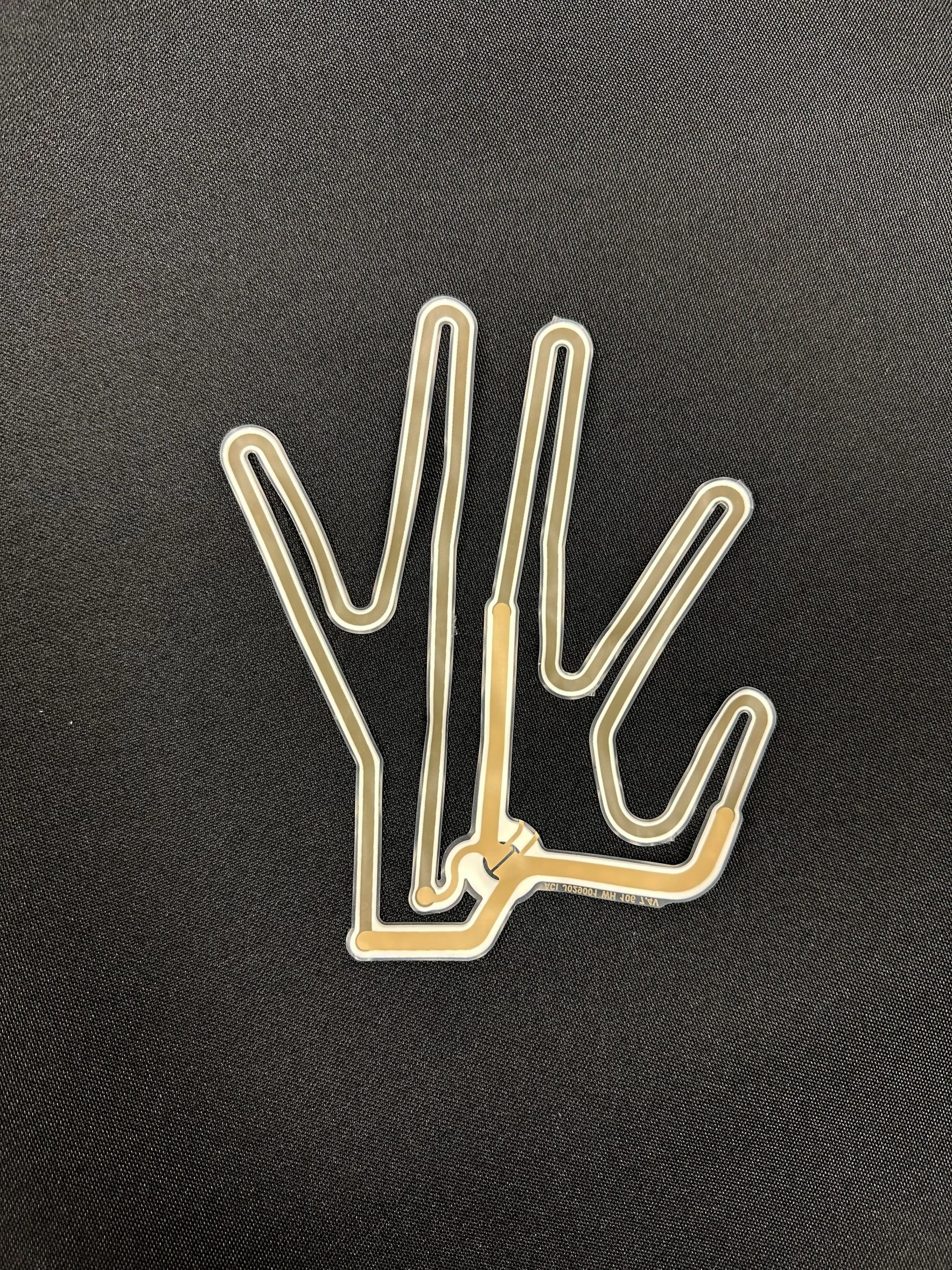
Wearable technology
Printed electronics are used in the production of wearable technology, such as smart clothing and fitness trackers. These products offer a high degree of comfort and flexibility and are lightweight and can be produced in many shapes or sizes including sensors that monitor heart rate, temperature, and other vital signs.
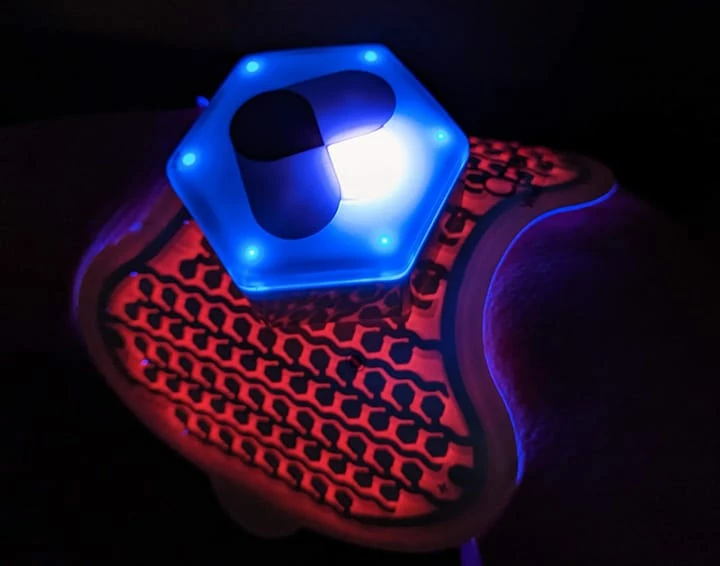
Printed sensor
Screen printing is commonly used to produce sensors for various applications, including medical devices, automotive, and industrial applications. The sensors can detect various parameters such as temperature, pressure, and humidity.
Automotive
Printed electronics can be used in automotive applications, such as in-mold structural electronics (IMSE®), molding the printed electronics into the final 3D part. Components can be embedded in the resin so there are no moving parts to fail.
Heated headlights for vehicles in colder climates are a great candidate for printed electronics. Watch our ice melt demo using a heated headlight printed at DuraTech.
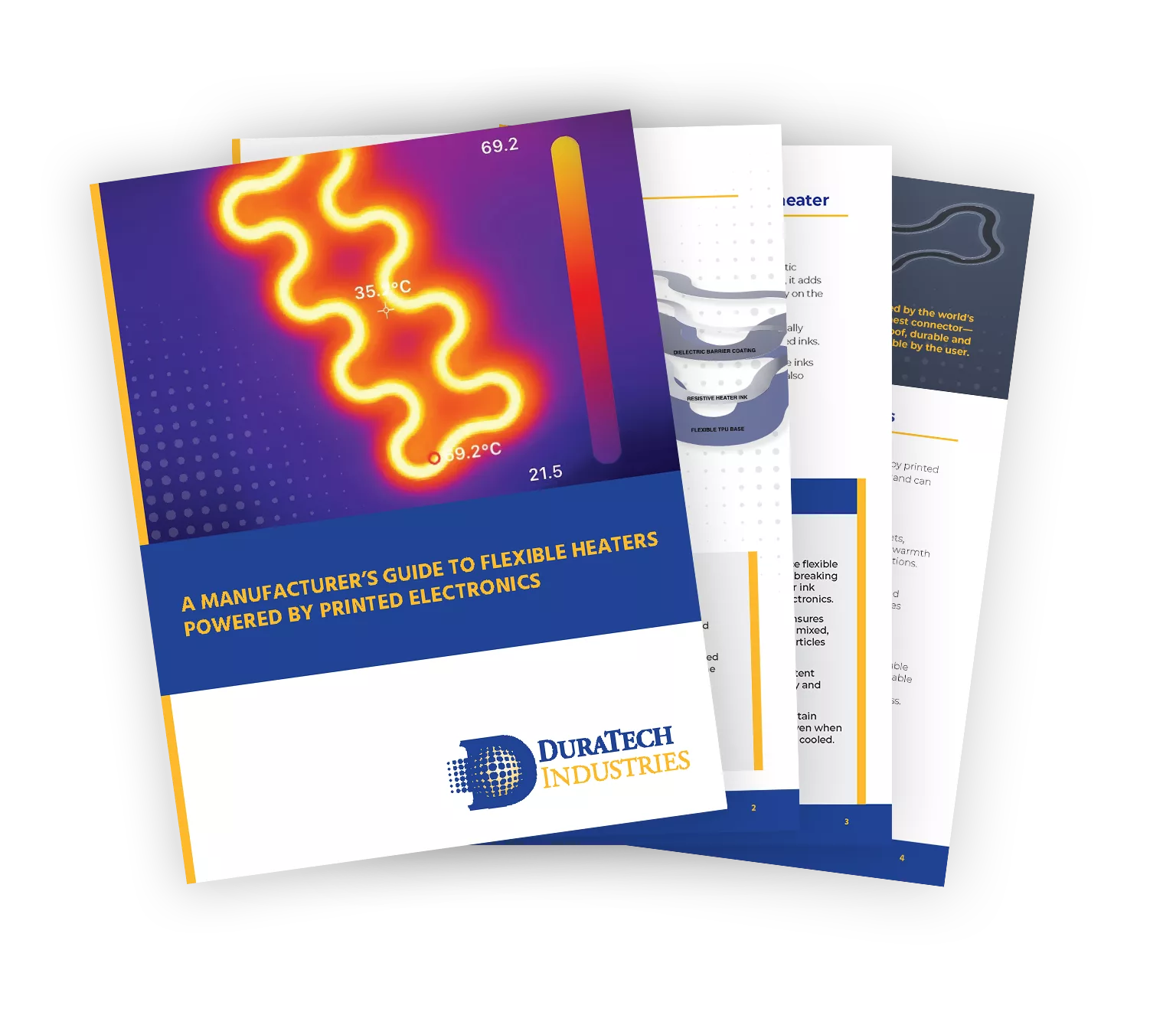
Ebook: A Manufacturer’s Guide to Flexible Heaters Powered by Printed Electronics
Imagine a wearable heating element that’s inconspicuous, comfortable, that flexes and flows with the fabric. This concept is not a futuristic vision; it’s here and DuraTech can help you bring it to market.
DuraTech creates human-friendly heating elements powered by innovative printed electronics. They integrate seamlessly into wearable technology and offer unparalleled design freedom for applications that require a conformable heat source.
Our flexible heating elements use revolutionary concepts in inks and films designed to stretch and conform. All-day comfort combines with safe, durable personal heating that holds up after dozens of wash cycles.
The benefits of printed electronics
Cost savings
Printed electronics products are cost-effective to produce, as they require fewer materials, less energy and less labor compared to traditional manufacturing methods. They are also lightweight and easy to transport, which reduces shipping costs. This makes it an ideal option for companies looking to reduce costs without sacrificing quality.
Design flexibility
Printed electronics offer a high degree of design flexibility, as they can be produced in many shapes or sizes. Engineers can create custom shapes, sizes and patterns, enabling them to create electronic devices that are unique and tailored to specific applications. This is especially important for user interface products, where the design can have a significant impact on user experience.
Sustainability
They are environmentally sustainable. They produce less waste and require fewer resources compared to traditional manufacturing methods. It is a global corporate responsibility to reduce the carbon footprint and promote sustainability.
Advantages of working with DuraTech
DuraTech has experts in printed electronics, in-mold structural electronics (IMSE), in-mold decorating (IMD), graphic overlays, labels, nameplates and insulators/gaskets. Our technical experts are with you through the entire process and can provide advice and assistance wherever needed. We print science℠
Featured Product
Domes
When constructing membrane switches, you have the option to include domes. A dome is essentially a button that completes an action (up, down, start, stop, etc.) when pressed.
Domes have four “feet” and a raised center. The four feet rest on what we call landing pads – the point of contact on the circuit. There is a fifth point of contact, which is where the raised center would make contact with when pressed down. This completes the circuit, thus sparking the desired action.
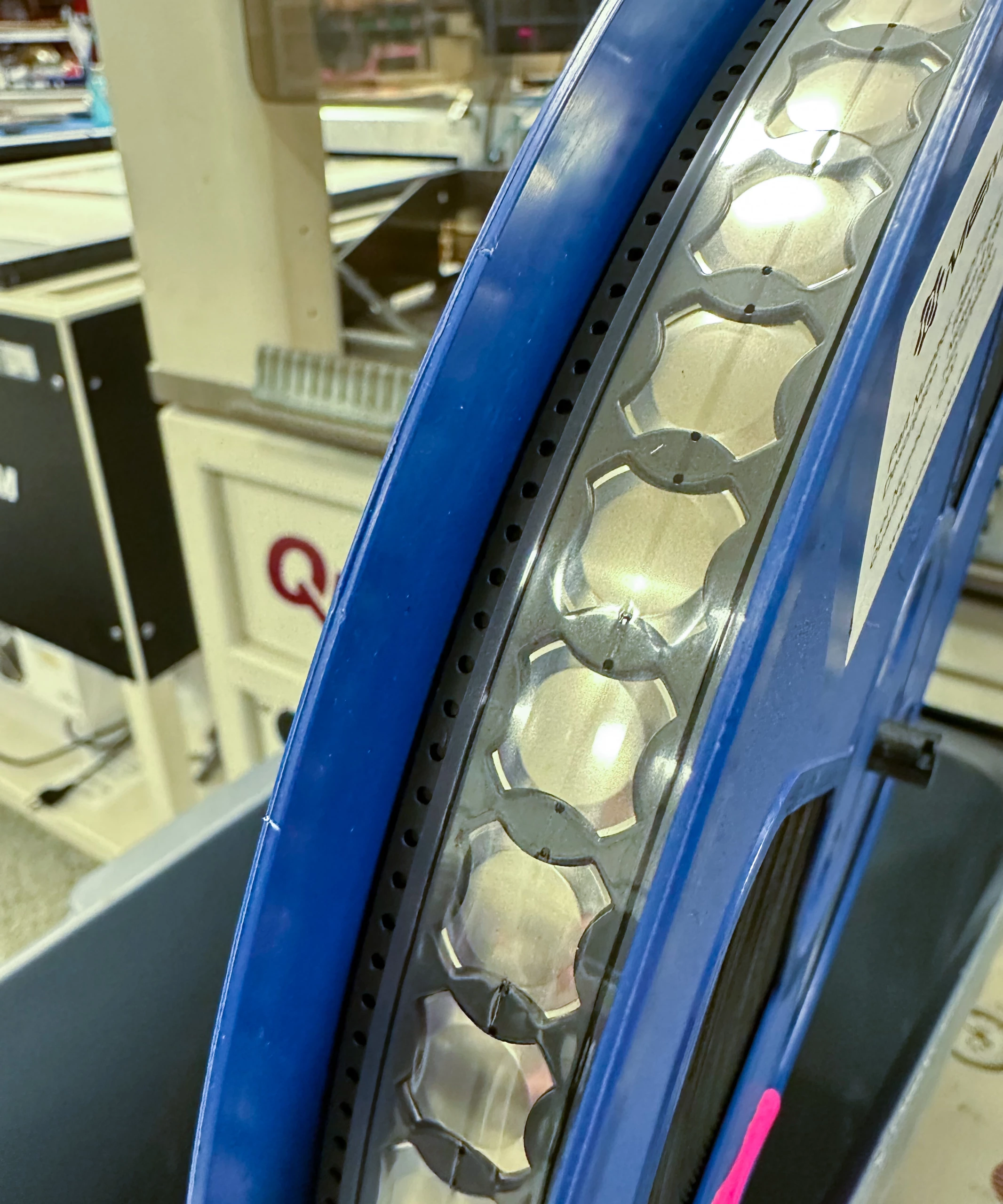
Dome options
Sizing – We offer sizes between 8.5 millimeters to 20 millimeters. The domes we carry are made of high quality stainless steel.
Actuators – To make pressing down on the dome easier, we can apply a dome actuator on top of the dome. This actuator guides force onto the dome, making it more sensitive to touch and requiring less precise pressure. We make the actuators in-house, so we can make them to your specifications.
Tactile Force – Domes come with a variety of tactile forces. If you seek a specific tactile force, our team can provide you with a solution.
Domes with Dimples – We offer domes with dimples. These are similar to our standard domes, but have an outward “dimple” underneath the raised center to get closer contact between the dome and the landing pad when pressed.
Domes with Holes – If your part requires an LED as part of the button structure, we offer domes with holes in the center. We place the LED underneath the hole in the dome for it to shine through, and the center of the dome will still make contact with the landing pad when pressed.
How Domes Are Applied
Domes are kept on a reel and fed through our Puma Pick-and-Place. They are automatically placed onto the part with accuracy and speed. The domes are aligned to the landing pads which are the points of contact that complete the circuit.